See How: TrySight Realized 90 Days Return on Investment using MfgPro230 xS SLS
Source: https://pro.xyzprinting.com/en-US/case-studies/TrySight
”The MfgPro230 xS is the first industrial quality SLS printer at a sub-industrial price point. It paid for itself in the first 3 months.” – President of TrySight, Umang Dua
BACKGROUND
TrySight develops various hardware and software solutions to help those with low vision and blindness. Its clients include educational institutions, hospitals and rehabilitation departments. TrySight is the leading Canadian manufacturer of magnification and reading systems for those with sight loss.
CHALLENGE
TrySight operates in a niche market where production runs are relatively low (50 to 1000 units). Additionally, design changes to parts are frequent. The combination of low production volumes with frequent design changes made traditional tooling methods uneconomical. Furthermore, TrySight needed a way to quickly iterate design changes to validate product concepts.
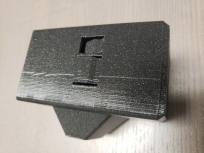
To address these challenges, TrySight was using FDM 3D Printing technologies for over 5 years for prototype as well as production parts. The quality of the parts TrySight was producing using FDM did not meet dimensional tolerances, strength or temperature resistance for end-use. Labor and material costs were significant due to high print failure rates and a two-dimensional build area which only allowed a few parts to be printed at a time.
The requirement for support structures on FDM parts required special considerations during the design process which was suboptimal. Furthermore, the parts lacked aesthetic appeal due to visible layer lines and resulted in a lower quality feel of the final product.
These limitations resulted in a low success rate for high value institutional contracts which cut into TrySights bottom-line and limited the overall growth of the business.
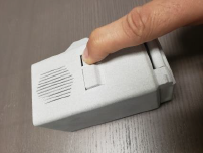
SOLUTION
TrySight had been searching for a better solution and decided to migrate its part manufacturing to the Selective Laser Sintering process. After six months of analysis and comparison with virtually all competing solutions, TrySight consulted with value added reseller, Objex Unlimited, to select the MfgPro230 xS owing to its quality, compact size, open materials ecosystem as well as the best price and performance ratio on the market.
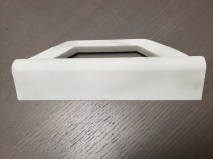
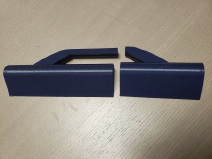
TrySight now designs its parts with very few design limitations as support structures are no longer required. Parts from the MfgPro230 xS are superior in virtually all aspects (Tensile Strength, Temperature resistance, Surface Finish etc.)
The ability to pack parts in three dimensions allows TrySight to manufacture dozens of parts per day with minimal failures thereby reducing labor costs.
Since parts that are used for prototyping are also used for production, there is no design effort to move from prototyping to production. Changes can be made instantly and released into production within hours instead of weeks with zero setup cost.
The Open Materials philosophy of the MfgPro230 xS has allowed TrySight to experiment with 3rd party materials to expand its offerings. Flexible parts using TPU allow for the manufacture of custom fit wearable products which is a capability not achievable by traditional manufacturing methods.
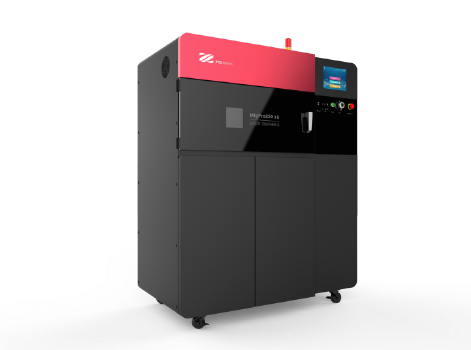
RESULTS / LOOKING AHEAD
The MfgPro230 xS has taken TrySight’s business to the next level with professionally produced short run parts that rival injection molding with no tooling cost. Additionally, the ability to produce bespoke parts allows TrySight to offer clients custom fit parts in a variety of materials which provides a unique competitive edge.
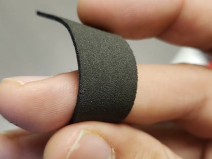
Leave a Reply
Want to join the discussion?Feel free to contribute!