Source: https://pro.xyzprinting.com/en-US/case-studies/TrySight
”The MfgPro230 xS is the first industrial quality SLS printer at a sub-industrial price point. It paid for itself in the first 3 months.” – President of TrySight, Umang Dua
BACKGROUND
TrySight develops various hardware and software solutions to help those with low vision and blindness. Its clients include educational institutions, hospitals and rehabilitation departments. TrySight is the leading Canadian manufacturer of magnification and reading systems for those with sight loss.
CHALLENGE
TrySight operates in a niche market where production runs are relatively low (50 to 1000 units). Additionally, design changes to parts are frequent. The combination of low production volumes with frequent design changes made traditional tooling methods uneconomical. Furthermore, TrySight needed a way to quickly iterate design changes to validate product concepts.
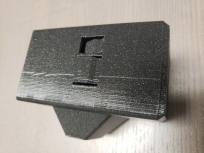
To address these challenges, TrySight was using FDM 3D Printing technologies for over 5 years for prototype as well as production parts. The quality of the parts TrySight was producing using FDM did not meet dimensional tolerances, strength or temperature resistance for end-use. Labor and material costs were significant due to high print failure rates and a two-dimensional build area which only allowed a few parts to be printed at a time.
The requirement for support structures on FDM parts required special considerations during the design process which was suboptimal. Furthermore, the parts lacked aesthetic appeal due to visible layer lines and resulted in a lower quality feel of the final product.
These limitations resulted in a low success rate for high value institutional contracts which cut into TrySights bottom-line and limited the overall growth of the business.
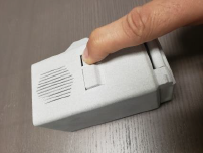
SOLUTION
TrySight had been searching for a better solution and decided to migrate its part manufacturing to the Selective Laser Sintering process. After six months of analysis and comparison with virtually all competing solutions, TrySight consulted with value added reseller, Objex Unlimited, to select the MfgPro230 xS owing to its quality, compact size, open materials ecosystem as well as the best price and performance ratio on the market.
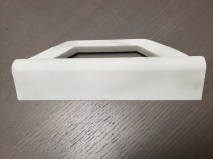
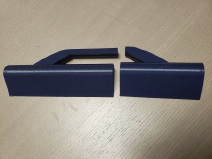
TrySight now designs its parts with very few design limitations as support structures are no longer required. Parts from the MfgPro230 xS are superior in virtually all aspects (Tensile Strength, Temperature resistance, Surface Finish etc.)
The ability to pack parts in three dimensions allows TrySight to manufacture dozens of parts per day with minimal failures thereby reducing labor costs.
Since parts that are used for prototyping are also used for production, there is no design effort to move from prototyping to production. Changes can be made instantly and released into production within hours instead of weeks with zero setup cost.
The Open Materials philosophy of the MfgPro230 xS has allowed TrySight to experiment with 3rd party materials to expand its offerings. Flexible parts using TPU allow for the manufacture of custom fit wearable products which is a capability not achievable by traditional manufacturing methods.
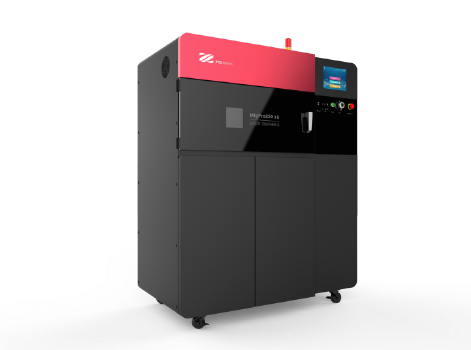
RESULTS / LOOKING AHEAD
The MfgPro230 xS has taken TrySight’s business to the next level with professionally produced short run parts that rival injection molding with no tooling cost. Additionally, the ability to produce bespoke parts allows TrySight to offer clients custom fit parts in a variety of materials which provides a unique competitive edge.
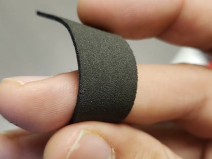
3D Printing in the retail space is nothing new, but we continue to see innovation in the footwear space, and how 3D Printing continues across more than just product design and development divisions.
At the forefront of the footwear industry, Adidas has been using 3D printing for years now and has even released shoes like The 4D run using cutting edge 3D printed midsoles. Nowadays brands like Reebok are utilizing advancements in full-color 3D Printing for promotional, marketing, and advertising material outside of just the product development stages.
Objex Unlimited was fortunate enough to work on this project for Reebok Canada to re-create miniature mockups of the release of The Zig for their recent viral Tik Tok campaign seen below:
The team at Reebok came to Objex Unlimited with a pair of “Zig’s”, and a concept of creating a miniature pair for their social influencers’ upcoming video campaign. They provided a few image examples and creative freedom on making it happen, and within a few weeks, we were able to deliver just that. A fresh pair of 3D Printed mini-kicks.
Here is the original Zig reference by Reebok:
The process looked something like this:
THE SHOE
- Since access to the CAD file was not readily available in time for their campaign we needed to create a 3D file from scratch. So we whipped up the digital asset to kick off the project. 3D scanning took place within a couple of minutes of having full access to the physical shoe. Our team was able to utilize our in-house Artec Eva and render up a 3D CAD file within a few hours. You can see the scan images below to get a better understanding of the data captured.
- Geometry was created using several stitched together scans
Geometry was created using several stitched together scans Using the Artec Eva we were able to capture a very details scan of the shoe.
- The texture was also captured during the initial scan output and processed using Artec Studio
Using the Artec Eva we were able to capture a very detailed scan of the shoe.
- Following scan capture, we ran a couple of test prints from the raw processed scan to see the quality of the original texture captured and its translation over to our new Mimaki 3D Printer. The results were pretty good but not quite perfect.
- This file was then brought into Zbrush where our team of digital sculptors cleaned up any imperfections in the geometry and added additional touchups to the model. Due to low light conditions during the scanning process, the vibrance of The Zig was not quite perfect. Our sculptors added additional saturation to the shoes’ orange hues, soles area, and logos to give that extra pop of colour.
- Our production team then reran the models on both the Mimaki 3duj-553 and the 3D Systems Project 660 to compare outputs and evaluate finishing options.
THE BOX
The second portion of the project consisted of a matching box to accommodate the pair of shoes. We produced a few variations in both traditional 2D and also 3D printing. Using the original box as a reference our sculpting team was able to replicate the design and graphics in zbrush for 3D production. You can see the final output below.
Q & A with President and CEO Vyomesh Joshi (VJ) on the New FabPro 1000
Source: 3D Systems
Following 3D Systems’ announcement of FabPro™ 1000, there has been a steady flow of interest around our take on industrial entry-level 3D printing: where FabPro fits into an additive manufacturing workflow, why we are investing in entry-level solutions, and how 3D Systems’ printer measures up to competing systems on the market. Eager to answer your questions, 3D Systems President and CEO VJ shares his view of the opportunities available through entry-level industrial printing with the new FabPro 1000.


The FabPro delivers parts that are on par with production level machines in terms of accuracy, quality and repeatability.
Q: HOW IS FABPRO™ 1000 DIFFERENT FROM OTHER ENTRY-LEVEL 3D PRINTERS ON THE MARKET?
VJ: The FabPro is distinct in several ways, but the most important distinction is the parts it prints. The parts are what matters at the end of the day, right? The combination of our printer and materials ensures part quality, repeatability and durability, so that’s the first key distinction. And of course, very closely related to part quality is part accuracy. The FabPro delivers better, more accurate parts than any other product at its price point and produces parts that are on par with production level machines in terms of accuracy, quality and repeatability.
The second differentiation is speed and productivity. FabPro is up to three times faster than competitively priced systems, which will help to make our customers more efficient and accelerate their time to market. Think about it: if it takes a competing system 9 hours to print apart but it takes our system just 3 hours to print a part with the exact same parameters, full days can be removed from product timelines. That’s a tremendous competitive advantage.
Finally, the FabPro is a complete, plug and play solution that includes rigorously tested, high-quality materials and an intuitive, optimized software experience with 3D Sprint.
BEYOND AFFORDABILITY, WHAT MAKES THIS AN ENTRY-LEVEL 3D PRINTER?
We want to help customers go from a CAD file to design verification or functional prototyping without jumping through hoops or needing extensive training, so we’ve made it very easy to use. Like our other professional quality printers, FabPro comes with 3D Sprint software for file preparation and print management. This gives users access to tools that help them optimize support structures and builds to reduce waste and also provides visibility into material usage. This combination of the fast print speeds I mentioned earlier and optimized printing delivers lower costs to our customers so they can continue to enjoy low operating costs after the initial purchase.
THE 3D SYSTEMS MISSION IS TO HELP MAKE 3D PRODUCTION REAL FOR CUSTOMERS. HOW DOES AN ENTRY-LEVEL INDUSTRIAL PRINTER FIT INTO THIS STRATEGY?
In order to make 3D production real for our customers, we need to make good quality and easy-to-use additive manufacturing solutions more accessible and affordable to help a wider audience adopt and benefit from the technology. In terms of how the FabPro does this, I will answer in two parts. The first half of my answer takes a look at the product itself. If you think about the product category – an industrial entry-level printer – it plays a very important role in making 3D production real. The FabPro 1000 is a solution with entry-level affordability that comes with industrial material capability and a significant speed advantage over other printers in its class. It also comes with 3D Sprint software to streamline the plastic additive manufacturing workflow, making it a complete solution. That means FabPro offers an opportunity for people to get hands-on with 3D technology for meaningful applications such as functional prototyping. Offering a low-barrier, quality experience that combines the right materials, the right hardware and the right software to compress product lifecycles reinforces how 3D Systems’ additive manufacturing solutions can help companies reduce design cycle time and develop complex custom parts not possible with traditional manufacturing processes.
The second half of my answer considers our customers globally, and the different price-performance capabilities and needs that exist worldwide. As a global company, 3D Systems works to serve all markets, including emerging geographies where an entry-level industrial printer like FabPro 1000 offers an optimal price-performance ratio with considerable benefits to the customer.


FabPro casting material enables users to achieve final metal parts with entry-level affordability.
I think the global designer community will be among the first to really understand and get excited about the capability being offered, but designers are not the only ones in need of an affordable yet professional-quality 3D printing solution. I think you have to consider other professions where the total package of benefits provided by the FabPro 1000 will make a difference. The combination of the materials we offer plus the high throughput and accuracy of the printer speaks to a wide range of users. If you need high durability functional prototypes, FabPro can do it; if you need high contrast material for prototyping intricate details, FabPro can do it. We also offer a casting material that will enable users to achieve final metal parts with entry-level affordability. This alone has the potential to transform verticals such as jewellery. I believe FabPro will complement and advance workflows across industries, and I am excited to see what our customers do with it!
3D Printing brings a whole new dimension to the world of engineers, fabrication and designers. We’ve discussed at length in previous articles the many misconceptions about the world of 3D Printing. In the following article, I’ll focus on the true value of having a 3D Printer in your workflow as an engineer or designer. Just like anything else, a 3D Printer is only one tool among many. But using the right tool for the right job will open new possibilities. It can cut costs, and most significantly, save time.
There’s a lot of hype in the consumer market right now. We all hear of big dreams of a 3D Printer of every home. But currently the technology really shines in prototype development. In particular, this is true for engineers and designers involved in new product development or the redesign of existing products. The ability to get your hands on prototype components, assemblies and complete products and review design issues, improvements and changes is quite simply, invaluable.
The speed of 3D prints
Whether you’re building a tool or fixture, designing a new product, or developing a prototype, as an engineer or designer, you need to fail often and recover quickly. As we know, creating the best possible part design usually requires multiple iterations and redesigns. Previously you would have to wait weeks or even months to see a physical version of your design. But now, 3D Printing has made it possible to get that part created the same day or the next day. This allows creators to print the design quickly, review errors or find improvements, make the changes to the file and print again within a very short time frame.
Today, you can go through 10 iterations in the same time it used
Complexity is free
This is a phrase you’ll hear thrown around quite a bit in the world of Additive Manufacturing (3D Printing). Traditional manufacturing processes have certain limitations. If you’re using milling or using CNC (Computer Numerical Control) to create a part, you’re removing material from the outside of your block of material and working your way inward. This means any kind of complex internal shape is usually impossible. A CNC machine cannot wrap around corners, but when you’re building from the bottom up, the 3D printer has no problem building organic, complex shapes and structures. If you’re using injection molding, you have to worry about hollow parts, drafting and maintaining wall thickness.
3D Printing doesn’t care about complexity. As long as you’re using some kind of support material system for your part – and using the right material and print method for the job – the complexity of your designs are virtually limitless. Please note that each individual printer will have it’s own limitations you’ll have to work within. However, having access to multiple printer technologies will give you a lot more freedom.
MarkForged Printers
Markforged offers a wide range of 3D Printers all specializing in creating parts strong enough for actual everyday use. Developed and manufactured in the United States, these are the only printers on the market that can print parts as strong as aluminum. Their printers generally use two printheads. One builds Nylon parts (or the amazing proprietary Onyx material). The other is a revolutionary new printhead that extrudes composite materials to reinforce the nylon to make solid, strong-as-aluminum 3D Prints. The composite materials used in the machine are Carbon Fibre, Fiberglass and Kevlar, and High-Strength High Temperature Fiberglass.
Markforged offers a range of options for those looking for more than the standard plastic-jet printers in the ‘prosumer’ price range. Starting at $3499 USD with the Onyx One 3D Printer. Even at its low price point, it has a place in the professional environment. It’s an excellent addition to the Engineer or Designer’s desktop (and totally safe for office use).
The printer ships with everything you need to get started. Including cloud-based Eiger software, giving you full control over customizing your 3D Printed composite fibre model. If you need more materials, you can opt for the Onyx Pro, which has the ability to reinforce with Fiberglass, or the Mark Two, which can print the full range of materials available. Additionally there’s the Mark X, which can print everything the Mark Two can print. However, it has a much larger build size and has a built in scanner to check the part for deficiencies during the print cycle.
Not sure if this printer fits your needs? Give us a call!
If you have any questions, want to see the printers in action, or are looking to order, please don’t hesitate to contact Objex Unlimited 3D Print Studio. You can also read more about the Markforged printers at www.objexunlimited.com
Products
Services
Join Our Newsletter
Objex Unlimited
2140 Dunwin Drive.,
Mississauga, Ontario L5L 1C7
Email: sales@objexunlimited.com
Phone: 416-233-7165
Mon – Fri
9am – 5pm EST