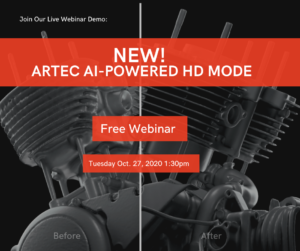
Learn about the latest and greatest in Artec Studio and the release of their new HD mode and AI-Powered 3D scanning features.
Steve Cory, 3D industry expert and founder of Objex Unlimited will review his experience with this new feature and discuss how it can revitalize your Artec 3D scanning equipment and workflow.
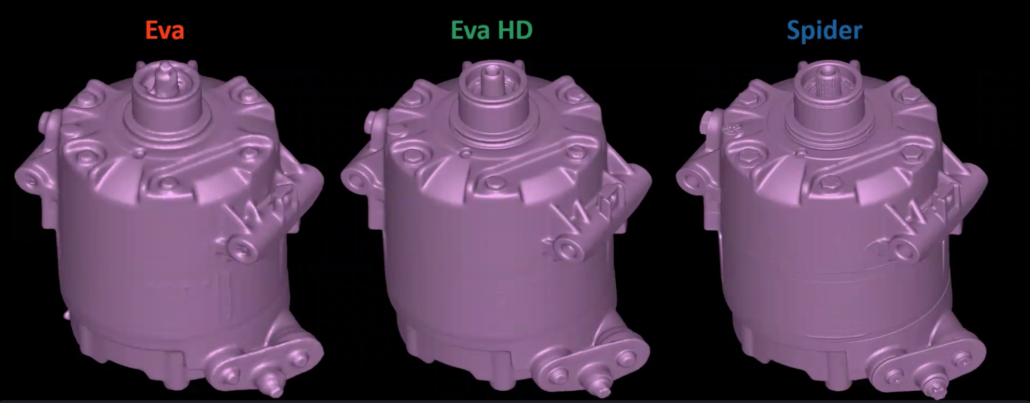
Source: https://www.artec3d.com/news/hd-mode-press-release
Santa Clara, Calif., October 14, 2020 – Artec 3D, a world-renowned developer and manufacturer of professional 3D hardware and software, today announces the successful development of a proprietary AI Engine that more than doubles the resolution of its Eva and Leo handheld scanners to 0.2 mm in a newly released HD Mode. Artec 3D is the first and only company to utilize deep convolutional neural networks to reconstruct 3D surfaces and improve the quality of 3D models. With HD Mode, users can create exceptionally accurate, low-noise scans of smaller, more detailed objects with complex surfaces, as well as large, intricate objects. HD Mode is free and available now for all Eva and Leo users via Artec 3D’s latest scanning and data processing software, Artec Studio 15.

“With the help of in-house developed training techniques and CNNs, we’ve managed to squeeze more information from the same amount of data captured from our existing 3D Eva and Leo scanners and get a much richer and denser representation of the scene being scanned,” said Gleb Gusev, CTO of Artec 3D. “Now we’re able to receive up to 64 times more measurements from the same scanners, which more than doubles the resolution of the final model and significantly decreases noise. Another advantage of our new approach is the much more accurate reconstruction of the surfaces this technique provides compared to standard algorithms.”
“We are committed to creating life-long Artec 3D users, not only by developing the industry’s most cutting-edge new 3D technologies, but also ensuring that the performance of our existing solutions is continuously being enhanced,” said Artyom Yukhin, President and CEO of Artec 3D. “The release of HD mode, powered by a first-of-its-kind neural network, is an extraordinary milestone for the 3D scanning industry that our users can benefit from right away. It’s incredibly rare for any company to release such a significant upgrade at no cost, but we want users to rest assured that when they invest in our technology it will continue to pay off for years to come.”
Artec 3D has a deep history in computer vision and AI, creating AI algorithms for its own 3D facial recognition devices, as well as for technology industry leaders. Most notably, Artec 3D’s team of AI experts worked with Apple to help develop its Face ID. Now, Artec 3D has leveraged its expertise to apply AI not only to 3D faces, but to 3D objects of any kind. The convolutional neural network powering Artec 3D’s AI Engine in Studio 15 software has been trained using millions of data points and hundreds of thousands of 3D models to ensure optimum performance in HD Mode.

When an Eva or Leo operator turns on HD Reconstruction, they can look forward to scans with unparalleled degrees of resolution, coverage, and detail. They can also select the desired density for HD scans, from a standard 1X all the way up to an astonishing 36X for Eva and 64X for Leo. To experience the benefits of HD Mode, users must utilize computers with NVIDIA GPUs and 2 GB (Eva) / 4 GB (Leo) of video RAM for proper scanning and data processing. NVIDIA is the Artec 3D recommended graphics card brand for Artec Studio users.
HD Mode allows users to scan more detailed objects in over twice the resolution, with Eva and Leo scanners. This mode easily captures sharp and thin edges in higher definition. Even complex structures with various hard-to-scan surfaces, such as those featuring holes and gaps, varying depths and angles, and recessed areas are now systematically reconstructed in every single frame to deliver the best possible scan. With HD Mode, tricky surfaces, such as those that are deep black, shiny, or covered in hair or fur, are also easier to digitize with incredible detail. HD mode has an elite level of noise reduction in both raw data and final model, making scanned objects ready for reverse engineering, as well as many other applications, without needing any editing.
To learn more about Artec 3D’s HD Mode, or visit www.artec3d.com/portable-3d-scanners/hd-mode.
3D Printing in the retail space is nothing new, but we continue to see innovation in the footwear space, and how 3D Printing continues across more than just product design and development divisions.
At the forefront of the footwear industry, Adidas has been using 3D printing for years now and has even released shoes like The 4D run using cutting edge 3D printed midsoles. Nowadays brands like Reebok are utilizing advancements in full-color 3D Printing for promotional, marketing, and advertising material outside of just the product development stages.
Objex Unlimited was fortunate enough to work on this project for Reebok Canada to re-create miniature mockups of the release of The Zig for their recent viral Tik Tok campaign seen below:
The team at Reebok came to Objex Unlimited with a pair of “Zig’s”, and a concept of creating a miniature pair for their social influencers’ upcoming video campaign. They provided a few image examples and creative freedom on making it happen, and within a few weeks, we were able to deliver just that. A fresh pair of 3D Printed mini-kicks.
Here is the original Zig reference by Reebok:
The process looked something like this:
THE SHOE
- Since access to the CAD file was not readily available in time for their campaign we needed to create a 3D file from scratch. So we whipped up the digital asset to kick off the project. 3D scanning took place within a couple of minutes of having full access to the physical shoe. Our team was able to utilize our in-house Artec Eva and render up a 3D CAD file within a few hours. You can see the scan images below to get a better understanding of the data captured.
- Geometry was created using several stitched together scans
Geometry was created using several stitched together scans Using the Artec Eva we were able to capture a very details scan of the shoe.
- The texture was also captured during the initial scan output and processed using Artec Studio
Using the Artec Eva we were able to capture a very detailed scan of the shoe.
- Following scan capture, we ran a couple of test prints from the raw processed scan to see the quality of the original texture captured and its translation over to our new Mimaki 3D Printer. The results were pretty good but not quite perfect.
- This file was then brought into Zbrush where our team of digital sculptors cleaned up any imperfections in the geometry and added additional touchups to the model. Due to low light conditions during the scanning process, the vibrance of The Zig was not quite perfect. Our sculptors added additional saturation to the shoes’ orange hues, soles area, and logos to give that extra pop of colour.
- Our production team then reran the models on both the Mimaki 3duj-553 and the 3D Systems Project 660 to compare outputs and evaluate finishing options.
THE BOX
The second portion of the project consisted of a matching box to accommodate the pair of shoes. We produced a few variations in both traditional 2D and also 3D printing. Using the original box as a reference our sculpting team was able to replicate the design and graphics in zbrush for 3D production. You can see the final output below.
Press Release: https://www.artec3d.com/news/artec-studio-15-scan-to-cad-release
Santa Clara, Calif., May 28, 2020 – Artec 3D, a world-renowned developer and manufacturer of professional 3D hardware and software, today announces the availability of Artec Studio 15, the latest version of its award-winning software. New Scan-to-CAD functionality allows for basic quality control and basic reverse engineering operations to be conducted directly in Artec Studio 15, saving users time and effort. For CGI artists, enhanced colour reproduction and model-to-model texture transfers will make creating life-like models even easier. In addition, boosted algorithms will ensure maximum accuracy and speed when scanning with Artec’s handheld, long-range and desktop 3D scanners.


“We’ve been told by customers that with every new Artec Studio release it is like receiving an upgraded scanner, which is something we are extremely proud of,” said Artyom Yukhin, president and CEO of Artec 3D. “Our advancements in 3D scanning algorithms help us outpace the industry in accuracy, speed and usability, while our growing number of features save users of all skill levels time. This year’s Scan-to-CAD features will create a huge leap in productivity for users conducting reverse engineering and inspection tasks.”
Enhanced User Experience


An array of new features and upgrades that boost accuracy and speed. New custom groups can now be created in Artec Studio 15, allowing users to work with multiple sets of data at the same time and organize them in custom folders. New automated workflows, including boosted Autopilot and more advanced auto-align functionality that is 2x quicker, next-generation texture registration, and faster project loading that now revolves around each scan having a dedicated CPU, will increase user productivity. A visually redesigned workspace and customizable interface allow users to tailor the software to their preferences.
While speed and accuracy have increased across all Artec 3D’s scanners with Studio 15, the smart scanning mode for the Micro desktop scanner is a game-changer. Objects can be digitized twice as fast as if done manually. By calculating the most effective scanning path, Smart Scanning Mode captures the optimal quantity of surfaces, using the least number of frames, to achieve fully automatic, ultra-high-resolution scans and at minimum size for fast processing.
New Quality Control Features


Users can now conduct quick quality control operations within Artec Studio by aligning scans to imported CAD models, including STEP, IGES and X_T formats. Fast surface distance map comparisons and micron-accurate measurements of all created 3D models allow for easy identification of inconsistencies between a scan and CAD model. Scans can also be fitted with CAD primitives, such as spheres, cones, planes and cylinders. This allows for highly accurate measurements to be taken between actual scans and these simple geometrical shapes. For more complex processes and tools, users can export to any full package inspection software, such as Geomagic Control X.
Boosted Reverse Engineering Functionality


Artec Studio’s CAD primitives also streamline workflows for reverse engineering. After a scan is completed, primitives can be used to extract key geometrical data in a CAD format which can be immediately used in SOLIDWORKS or other CAD software. In addition, Artec Studio 15’s Precise Positioning feature lets users position models in the world coordinate system. Correctly positioned models with primitives aligned to the scan data can be exported as popular CAD formats for an easy transition directly into SOLIDWORKS, Geomagic Design X and other CAD software.
Vivid Textures for CGI and More


With Artec Studio 15, users can rest assured that colour will be captured and displayed correctly thanks to multiple automated features. Without manually predefining the area of application, the software filters out unwanted colour data from behind an object. The strength of this feature can be adjusted using the suppression level slider. Refined algorithms search across multiple scans for correct colour substitutes. This feature works similarly to the popular Glare Reduction tool. Another time-saving feature is model-to-model texture transfer. Users can clone textures from existing models and transfer them directly to new models.
This article was initially published in the July 2015 Issue of Graphic Arts Magazine.
Whatever your application may be, the one thing you will always need for ANY 3D print is a functional 3D design file. You can design the file from scratch using CAD (or any of the various 3D design software programs), but you’ll quickly discover that this process is labourious and requires a very advanced set of skills. One of the best ways to kick-start your design process is to utilize 3D scanning technologies. Additionally, there are a variety of applications where you can utilize 3D scans for modelling and visualizing in the digital realm. This column will cover some of the 3D Scanning Basics you need while entering this world.
3D scanning uses a device that analyzes a real-world object or environment to collect data on its shape, texture and (in some cases) colour. Certain devices are handheld and hover around the object to obtain a collection of snapshots that are stitched together to create a full three-dimensional model. Other devices affix the scanner to a tripod and use a turntable to rotate the object. Some devices are in the form of a chamber or booth, with the object or person positioned in the center as they’re scanned from multiple angles. Finally, there are scanners that can be attached to an aircraft or vehicle to capture entire landscapes. No matter what form a 3D scanner takes, it will give you a huge leg up on developing your design.
Why use 3D Scanning?
On the most basic level, 3D scanning is a quick and effective way to capture the geometry of an existing object, which will aid in the design of new items and fixtures, applying an extension or new part to an existing geometry, or in reverse engineering applications. If you’re designing a part to be used for some pre-existing device (for example a vehicle, tool or machine), you can quickly capture the dimensions and measurements of a physical object and be confident your parts will fit together on the first try. You can enhance or change an existing part you’ve created, or digitize parts that were built before CAD software became widely used. You’ll see 3D scanning in the field of biometrics, obtaining 3D data for the design of prosthetics and implants, and increasingly used in the field of graphics and VFX, providing digital assets in the creation of 3D animations. 3D scanning is also being used more and more as a means of historical preservation. In fact, many objects from our past which are starting to show the effects of time can be digitally stored and maintained, or replicated through 3D printing. There’s an endless list of possibilities for 3D scanning and new ones are popping up every day.
3D Scanning Technologies
As you’ll soon realize, as with many things in the realm of 3D, there is no one-size-fits-all solution when it comes to 3D scanners. So it’s best to figure out your particular needs and choose a scanner that suits your specific application.
Structured Light Scanning. These 3D scanners project a pattern of lights onto an object. The scanner then reads the reflections in the light to analyze curves and bends in the surface of the object. These scanners are flexible to use, good for many applications and safe on human eyes. These are generally a lower cost, but are not optimal on reflective or refractive surfaces.
Laser Scanning. These 3D scanners function similar to Structured Light, except they use lasers instead of a blanket of light. These can be great for precise engineering applications and capturing fine details, but are unsafe for human eyes. Thus they need to be used in a controlled environment.
Photogrammetry. This method uses multiple cameras to capture the object from different angles along with an algorithm that triangulates common points to analyze depth and create a 3D model. It gives you the best colour detail, however is not the most accurate for making precise measurements.


Objex Unlimited President and Founder Steve Cory inside the Selftraits Photogrammetry 3D Scanning Booth
Also worth mentioning are MRI/CAT scans which are used in medical applications to scan inside an individual’s body. And CMM machines – though technically not 3D scanning – use a physical probe to get precise dimensions of an object.
The Artec Eva 3D Scanner
One of the 3D scanners we often recommend is the Artec Eva handheld Structured Light Scanner. While it won’t be the optimal scanner for every situation, it is certainly one of the most versatile and easy-to-use scanners on the market and is priced very competitively. The Eva doesn’t require markers or calibration. It captures objects quickly in high resolution and vibrant colour at up to 16 frames per second. These frames are aligned automatically in real time, which make scanning easy and fast. Please contact us at Objex Unlimited for a demonstration, or to answer any questions.
About Objex Unlimited
Objex Unlimited 3D Printing Studio is a 3D solutions provider and 3D product reseller specializing in 3D Printing, 3D Scanning, 3D Design and 3D Services. We’re leading the 3D printing revolution to explore, develop, and commercialize new applications in 3D. Leveraging unparalleled expertise in 3D technologies, we work with you personally to find a product or solution that will save you time, effort, and money. We will bring your ideas and designs to life by creating working parts, beautiful full-colour models, and rapid prototypes. Authorized resellers of 3D Systems, Artec, Markforged and LMI Technologies.
Originally posted on Artec3d.com
Great news! If you’re looking for a 3D scanner for design, QA or engineering jobs, you now have another good reason to go for Artec Spider, and if you already own a Spider, here’s a fact confirming you made the right choice – the world’s #1 web portal for mechanical computer aided design, MCADCafé, has named Spider the best hardware showcased at SolidWorks World 2015 in Phoenix, AZ. The competition was really tough, with over 100 exhibitors bringing their products to the show, and this makes the award especially valuable.
Here’s what the editor-in-chief of MCADCafé, Jeff Rowe, who has over 35 years of experience in industrial design and engineering, has to say about Spider: “Although about a year old, we’d never seen this 3D scanner up close until this week at SolidWorks World. What impressed us most was the unit’s capture speed and quality, as well as its portability.”
To find out what else impressed Rowe about Spider and which product was chosen the best software, read Rowe’s review.


Products
Services
Join Our Newsletter
Objex Unlimited
2140 Dunwin Drive.,
Mississauga, Ontario L5L 1C0
Email: sales@objexunlimited.com
Phone: 416-233-7165
Mon – Fri
9am – 5pm EST